During high-speed forward flight of rotorcraft, flow separation on the rotor blades induces severe vibratory aerodynamic loads. Therefore, active control of flow separation is an important consideration for extending the operating envelope of the aircraft. However, vibratory loads are also prevalent in the absence of separation in cruise and descent conditions where the angle of attack on the blades is low or moderate, and the vibrations in this flight regime are primarily due to complex interactions between unsteady 3D flow and rotor blade structural dynamics. Because the effectiveness of leading-edge fluidic actuation approaches that are designed for manipulating separated flow diminishes at moderate and low angles of attack when the base flow is nominally attached, manipulation of the aerodynamic loads for vibration control was sought using fluidic actuation near the trailing edge. While past efforts in on-blade vibration reduction mainly focused on mechanical actuation, fluidic actuation could be a lighter and more efficient alternative because it is unhindered by complex electro-mechanical moving surfaces.
In the present experiments, the aerodynamic loads on a VR-12 airfoil are bi-directionally controlled at low angles of attack using independent bi-stable fluidically switched jet actuators integrated into the suction and pressure surfaces (SS and PS, respectively) near the trailing edge. It is shown that steady PS or SS actuation can lead to bi-directional increments or decrements in lift that are similar to the effects of trailing edge deployable gurney flaps but at a significantly lower drag penalty. Such time-dependent (pulsed) actuation simulates the effects of deployable microflaps and maybe exploited for flapless aerodynamic maneuvering and on-blade vibration control.
The design of the novel trailing edge pulsed switching actuator draws inspiration from fluidic computer concepts first originated in the 60s. This design utilizes a fluidic mechanism that is similar to a bi-stable, Coandă wall-attachment fluidic amplifier within an internal diverging nozzle. A steady primary jet interacts with two alternating diverting control jets (each 0.05-0.1 of the flow rate of the primary jet) within the nozzle that leads to two outlets corresponding to either (nominally) tangential or normal (60° relative to chord) blowing over the airfoil’s surface as depicted by the following schematics.
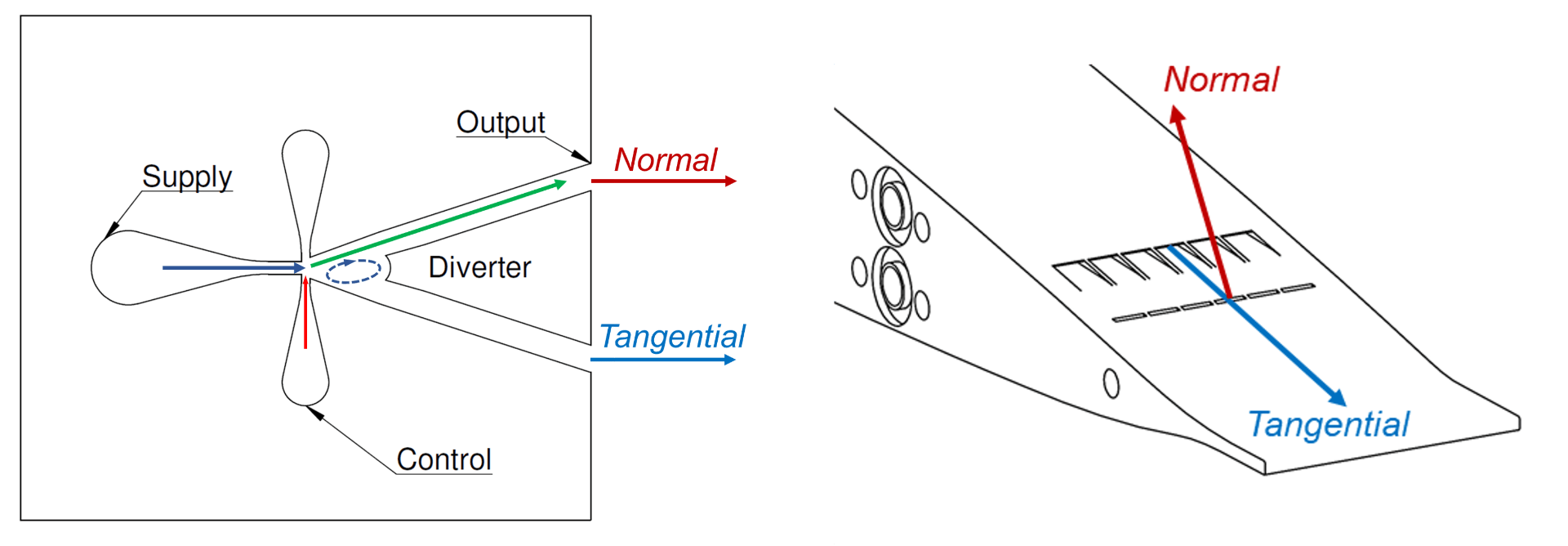
The actuation jet of a bench top module in a quiescent environment was visualized during the switching process on both SS and PS using high-speed Schlieren imaging (2,000 fps) and the results are played at 1/50x speed in the videos below. In the left video, the SS and PS actuation jets are simultaneously switched from the tangential to normal outlets, while the right video shows alternating switching of SS and PS jets. This benchtop module demonstrated that the current design for the novel fluidic actuator can yield an instantaneous momentum coefficient of up to Cμ = 3.03% (based on U∞ = 20 m/s) at switching frequency exceeding 30 Hz.

The bi-directional control authority of the switching actuator is investigated with time-dependent measurements of the global lift, moment and drag coefficients and time-resolved phase-lock PIV near the mid-span plane. The results here are representative of a typical application scenario of the pulsed switching actuator for vibration control, where the actuators are programmed to modify the lift and pitching moment in a square wave pattern. This is achieved by switching on the normal jets on SS and PS sequentially as shown in the PIV.
At the beginning of the cycle when both jets are in their tangential outputs, there is a negligible effect on the lift and a small increase in the pitching moment. With the PS jet switching to normal output, the free stream is significantly deflected downward with a closed circulation bubble forming on the windward side of the actuation jet. Also, the actuation jet entrains a significant amount of flow from the freestream and vorticity from the suction side, increasing the circulation around the airfoil. The combined result is a sharp increase in the lift coefficient of up to 0.4. When SS jet switches to normal output nearly the opposite effect is observed by the PIV resulting in a decrease of lift coefficient of almost 0.8 (or 0.4 below baseline levels) in a short span of 7 Tconv. The flow relaxes to the base flow when normal actuation is terminated. Pitching moment exhibits the same square wave pattern with decrease and increase of -0.04 and 0.05, respectively. Last but most importantly, as seen from the CD – α curve, the drag coefficient remained below baseline levels during the entire time when the fluidic actuation are active. This is quite a significant advantage over mechanical control surfaces where instead of incurring a drag penalty, switching jet actuation near the trailing edge can effectively decrease the drag coefficient in both tangential and normal output configurations.