Robot-assisted Online Monitoring & Maintenance
Operation and Maintenance (O&M) costs make up almost 66 % of the total operation cost of Nuclear Power Plants. Total O&M costs are expected to continue to increase as plants age. With the rapid development in Robotics and Autonomous systems, we strive to put a dent to these expenses by deploying mobile robots which can carry out basic walk-down and maintenance tasks with limited to no supervision. We are currently transferring a 2D simulation to a 3D simulation for robotic trajectory optimization and path planning.
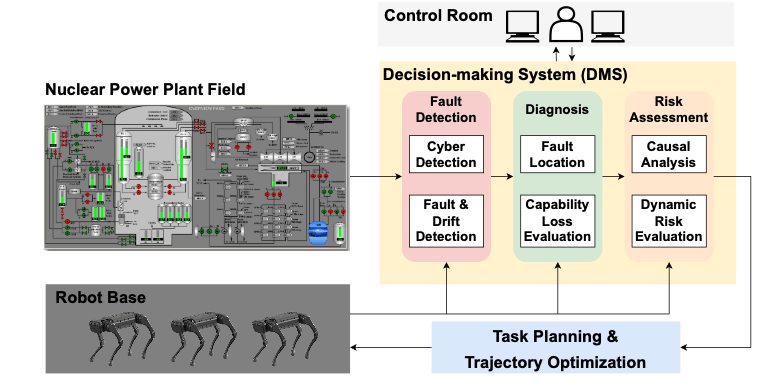
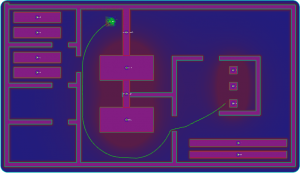
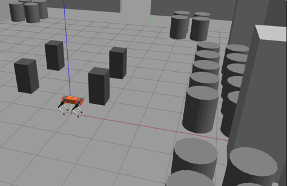
Nuclear Power Plant Digital Twin for Robots and Autonomous Intelligence
Robotics is playing a growing role in the nuclear industry, improving automation and efficiency. However, as robots become more complex, better simulation and control methods are needed to predict their behavior and optimize plant performance. Existing digital twins often focus on specific subsystems, limiting their usefulness for broader research.
To address this, we are developing a full-scale nuclear power plant digital twin in Unreal Engine 5, integrated with a high-fidelity General Pressurized Water Reactor Simulator. This system provides real-time monitoring, predictive maintenance, and a dynamic virtual environment. With built-in features like a Python bridge, it enables researchers to test custom algorithms. Applications include multi-robot task scheduling and navigation in radiation-exposed areas, demonstrating its potential for advancing nuclear robotics.


Multi-Objective Robot Path Planning
Radiation surveys can be conducted with robotic platforms. Two factors trade off each other in implementing robotic radiation survey: radiation exposure to robots & information gain from a survey. It is essential to keep as low radiation exposure as possible while gaining sufficient information. This can be regarded as a multi-objective problem. This research develops a robot path planning policy to balance these two objectives.
Enhanced Virtual Reality Platform for Training in Nuclear Power Plants
Virtual Reality (VR) technology offers numerous benefits for nuclear power plant training. By transitioning from traditional on-site training to VR-based simulations, nuclear facilities can significantly reduce expenses associated with in-person instruction, specialized equipment, and potential production downtime. Moreover, this approach allows trainees to practice handling critical situations and rare events in a risk-free environment.
This platform includes two unique features: Large Language Model (LLM) ChatBot and Personal Report System. The LLM ChatBot guides trainees through scenarios, answers questions, and provides feedback based on the trainee’s actions and decisions. The Personal Report System generates an individualized report, which is based on the trainee’s performance and interactions with the LLM ChatBot.
Currently, we are expanding the range of nuclear power plant scenarios, developing LLM ChatBot and Personal Report System implementation.

Teleoperation of Robots using VR
The integration of virtual reality (VR) technology with teleoperated robots represents a significant advancement in remote control systems. This innovative project combines the immersive capabilities of VR with the versatility of robotic platforms, enabling operators to control robots in distant or hazardous environments as if they were physically present.
We have developed a 3D VR-compatible environment using Unreal Engine, which provides a highly detailed and realistic virtual representation of the robot’s surroundings. Currently, we are working to integrate control part of the robot with VR controller.
